¿Cuál fue el reto o problema a resolver?
Este proyecto surgió de la necesidad de un cliente de aplicar el marcaje láser en unos moldes metálicos con geometrías de alta complejidad. Estas piezas, sin posibilidad de reemplazo, requerían de un proceso que garantizara cero errores mientras se conseguía mejorar sus propiedades y así volver a reintegrarlas, en tiempo récord, a la línea de inyección de nuestro cliente.
Se trataba de un desafío ya que cada superficie de cada pieza debía estar perfectamente centrada y enfocada por el láser, una tarea complicada dada la diversidad de superficies, orientaciones y alturas que tenían las piezas.
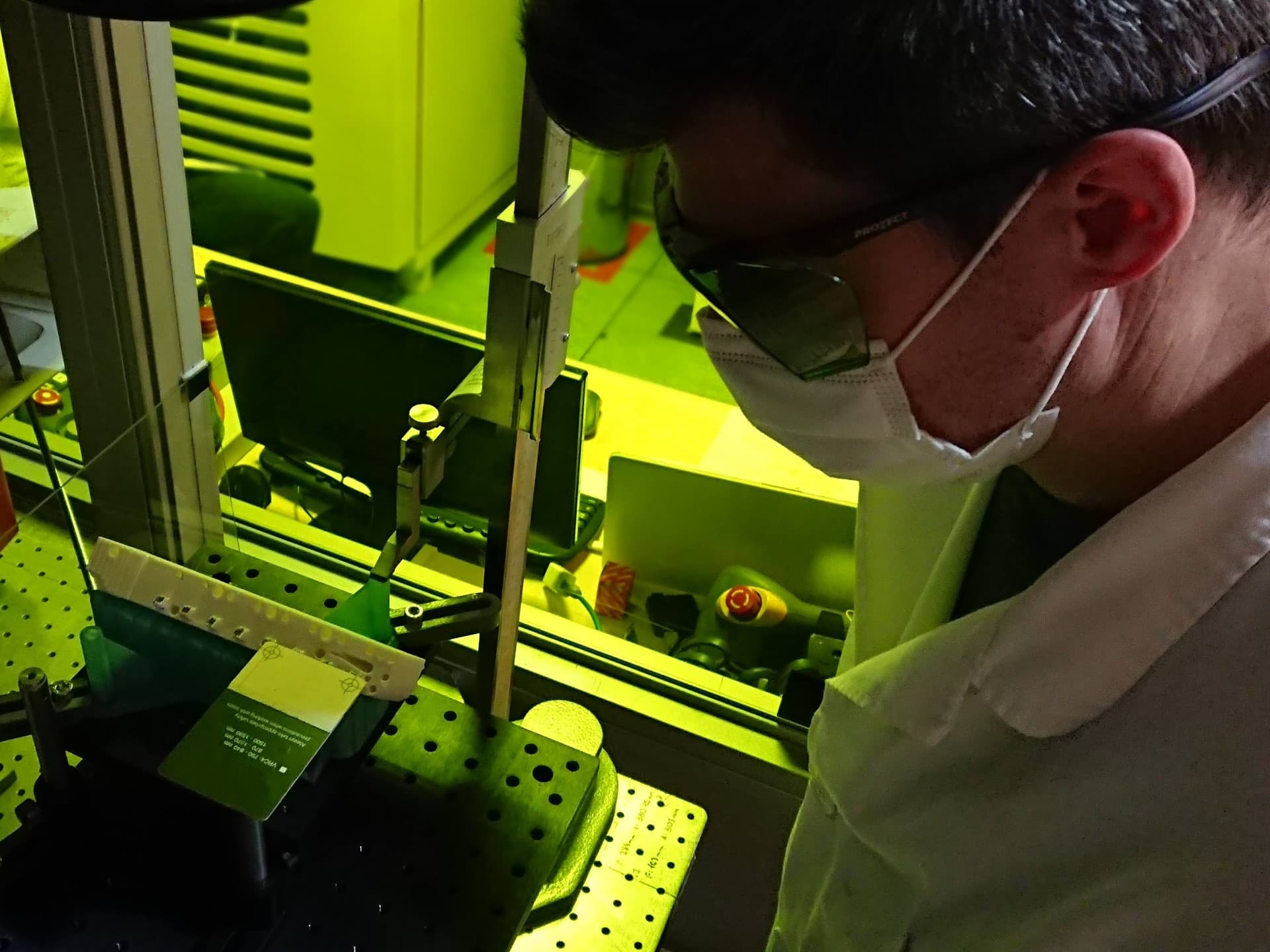
La propuesta del equipo de Desarrollo de producto fue diseñar una solución a medida que redujera el tiempo total y los posibles errores durante el procesado de los moldes.

Este enfoque permitió al equipo de Desarrollo de Producto comprender las limitaciones del equipo láser, incluyendo los rangos máximos de desviación que el proceso podría tolerar sin comprometer la calidad de las piezas a procesar.
Con esta información como base, el equipo procedió al diseño de utillajes específicos, empleando un proceso iterativo para afinar su funcionalidad. La utilización de modelado 3D y herramientas de metrología jugó un papel crucial en esta etapa, facilitando la precisión y eficacia del diseño hasta alcanzar la solución óptima. La producción de duplicados de las piezas originales a través de impresión 3D y la creación de prototipos de los útiles diseñados permitieron llevar a cabo pruebas preliminares esenciales, mitigando cualquier riesgo potencial sobre las piezas finales.
En la fase final del proyecto, se implementaron mejoras significativas en el diseño de posicionamiento fino, aprovechando la metodología poka-yoke para eliminar cualquier posibilidad de error. La impresión 3D de los útiles definitivos marcó un hito importante, preparando el terreno para las pruebas finales en el laboratorio láser. Una vez montado y testeado el sistema en condiciones reales, se confirmó su eficacia, asegurando que todo estaba listo para el procesamiento final de las piezas por parte del cliente.
Esta metodología de desarrollo de útiles (análisis técnico detallado, innovación en diseño y pruebas exhaustivas) no solo permitió reducir el tiempo total de procesamiento de semanas a días, sino que también garantizó una total ausencia de errores, cumpliendo y superando las rigurosas expectativas del cliente.