What was the challenge or problem to solve?
This project arose from a client’s need to apply laser marking on metal molds with highly complex geometries. These irreplaceable pieces required a process that guaranteed zero errors while improving their properties and thus reintegrating them, in record time, back into our client’s injection line.
It was a real challenge, as each surface of each piece had to be perfectly centered and focused by the laser, a complicated task given the diversity of surfaces, orientations, and heights of the pieces.
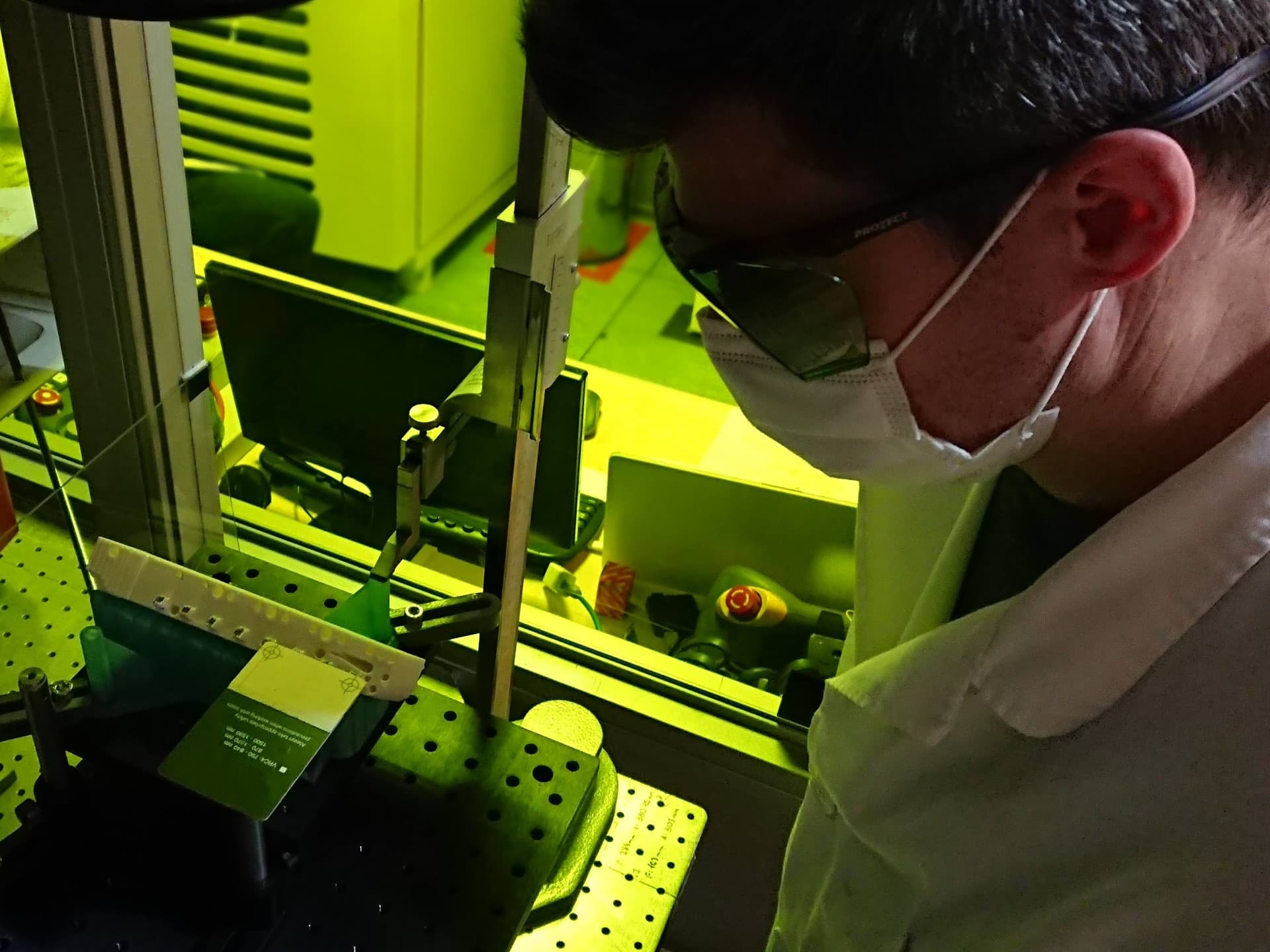
The laser marking of the molds ran the risk of being slow and error-prone, threatening to halt the production line for weeks, an unacceptable situation for any company in a competitive market.
The Product development team’s proposal was to design a customized solution that reduced the total time and potential errors during the molds’ processing.

The process began with an exhaustive analysis of the laser specifications and the complexities inherent to the geometries of the pieces. This analysis was complemented with detailed interviews with laboratory technicians specialized in laser, along with a series of initial tests using 3D models. This approach allowed the Product Development team to understand the limitations of the laser equipment, including the maximum deviation ranges the process could tolerate without compromising the quality of the pieces to be processed.
With this information as a foundation, the team proceeded to design specific tooling, employing an iterative process to refine its functionality. The use of 3D modeling and metrology tools played a crucial role in this stage, facilitating the precision and efficiency of the design until the optimal solution was reached. The production of duplicates of the original pieces through 3D printing and the creation of prototypes of the designed tools allowed for essential preliminary tests, mitigating any potential risk to the final pieces.
In the final phase of the project, significant improvements were implemented in the detailed positioning design, leveraging the poka-yoke methodology to eliminate any possibility of error. The 3D printing of the definitive tools marked an important milestone, preparing the ground for the final tests in the laser laboratory. Once the system was assembled and tested under real conditions, its effectiveness was confirmed, ensuring everything was ready for the final processing of the pieces by the client.
This tool development methodology (detailed technical analysis, design innovation, and exhaustive testing) not only allowed for a reduction in the total processing time from weeks to days but also guaranteed a total absence of errors, meeting and exceeding the client’s rigorous expectations.