Mechanical properties
The mechanical properties of a material are those that affect its mechanical resistance and its capacity when a force is applied to it. In other words, mechanical properties are those properties that a material possesses that are related to its ability to transmit and resist forces or deformations .
These properties are of utmost importance, since those materials intended for engineering products must have an optimum mechanical resistance to be able to work under different forces or loads. At Infinitia Industrial Consulting we offer you with our laboratory a wide range of tests to study these factors.
Main mechanical properties
Within this field there are a multitude of properties that can be measured. Some of the most common are the following:
Resistance
It opposes the deformation or rupture of the material in the presence of external forces or loads.
It is the capacity of a material to absorb energy and deform plastically without fracturing.
It is the ability to resist change permanently due to external stress.
Fragility
Indicates the ease with which a material fractures when subjected to a force or load.
The ease with which a material deforms under compressive stress in sheet form.
Ductility
The deformation under stress of a material. Most common steels are quite ductile and can withstand local stress concentrations. In contrast, brittle materials, such as glass, cannot withstand stress concentrations because they lack ductility and fracture easily.
Fluence
The tendency of the material to move slowly and deform permanently under the influence of external mechanical stress.
Resilience
It is the ability of the material to absorb energy when elastically deformed by applying stress and release the energy when the stress is removed. The tested resilience is defined as the maximum energy that can be absorbed without permanent deformation.
Fatigue
This is the weakening of the material caused by repeated loading of the material. When a material is subjected to cyclic loading and loads above a certain threshold value, but well below the material’s strength, tensile strength limit or yield strength, microscopic cracks begin to form at grain boundaries and interfaces. Eventually, the crack reaches a critical size. This crack propagates suddenly and the structure fractures.
Contact with us
receive a tailored professional response
Testing of the mechanical properties of materials
Materials testing measures the characteristics and behavior of metals, ceramics or plastics under various conditions where they are subjected to forces and stresses. The data obtained can be used to specify the suitability of the materials studied in various applications or to modify them for optimal use.
Testing can be used to detect defects in components, structures or machines that are failing, such as fractures or deformations due to forces and stresses, and to correct them.
There are different forensic engineering tests that can be performed in specialized laboratories, such as Infinitia’s, to test material properties or solve structural problems. Here are some of them:

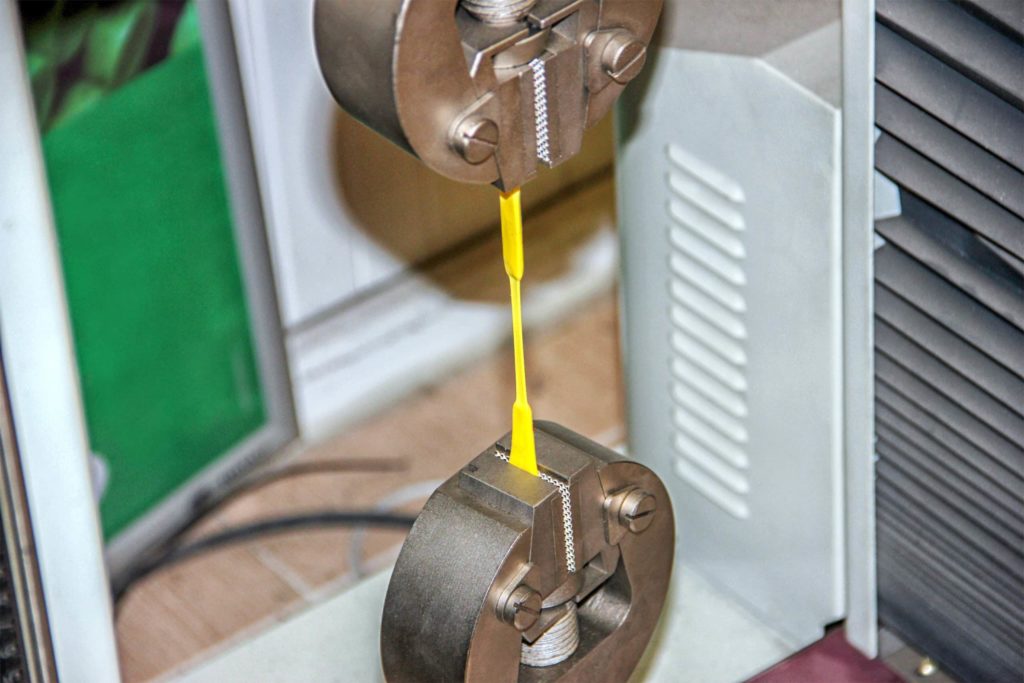
Static tension and compression tests
When a material is subjected to stress, it eventually breaks. A static tension test determines the breaking point of the material and its deformation.
In the static tensile test, the machine uniformly stretches a small part of the workpiece. The length of the test section (called the gauge length) is measured at different loads with a device called an extensometer; these measurements are used to calculate the strain.
Static compression tests determine the response of a material to crushing, or support-type loading, as in the beams of a house. Testing machines and extensometers for compression tests resemble those used for tensile tests.
Fracture resistance tests
These are quantitative tests capable of measuring the propensity of a material to propagate a crack. Tests have shown that cracks occur by opening, when two pieces of the material separate in the vertical plane; by edge slip, when the material splits in the horizontal plane; and by tearing, when the material splits with one piece moving diagonally upward and the other diagonally downward.
When using a material intended for a certain use, we must make sure that fractures will not occur. For this reason, analyses are carried out on how the materials break. For example, in the case of metallic conductors , the cause of fracture is established and, ultimately, their redesign is carried out.
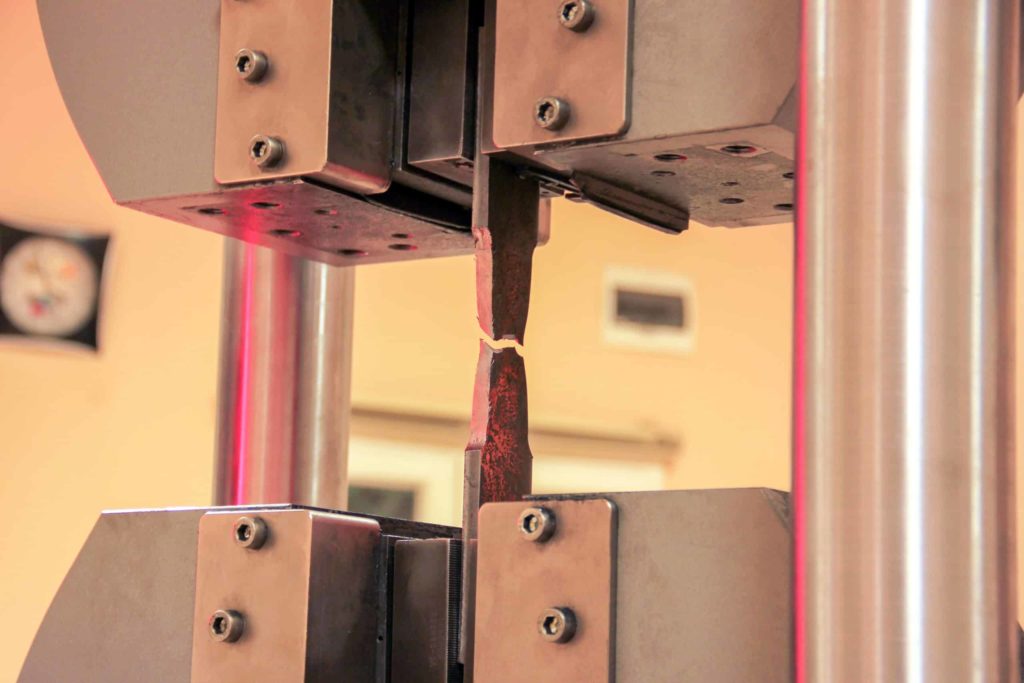
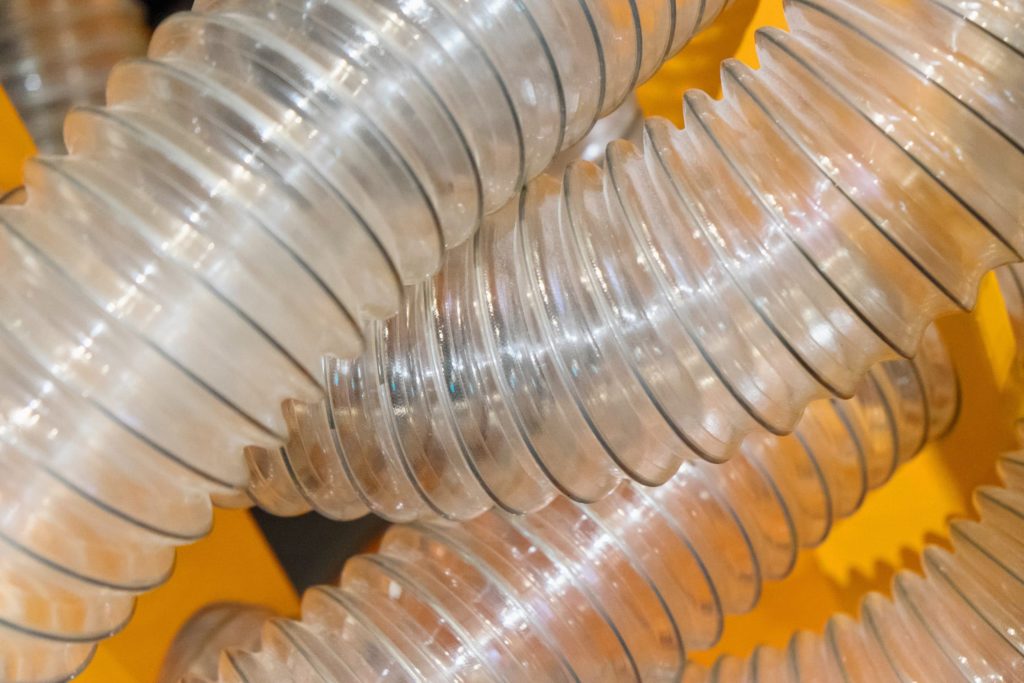
Shear and bending tests
In-plane shear tests indicate the deformation response of a material to tangentially applied forces. These tests are mainly applied to thin film materials, either metals or composites, such as glass fiber reinforced plastic.
A homogeneous material, such as untreated cast steel, reacts differently under stress than a granular material, such as wood, or a glued joint. These anisotropic materials are said to have preferential planes of weakness; they resist stress better in some planes than in others and should therefore be subjected to a different type of test.
Tensile tests are difficult to perform directly on certain brittle materials, such as glass and ceramics. In these cases, a measure of the tensile strength of the material can be obtained by performing a bending test, in which tensile stresses (stretching) are developed on one side of the bent member and corresponding compressive stresses on the opposite side.
Hardness test
Based on the idea that the response of a material to a load placed on a small point is related to its ability to deform permanently (yield), hardness testing is performed by pressing a hardened steel ball (Brinell test) or a steel or diamond cone (Rockwell test) on the surface of the test piece. Similar indentation tests are performed on wood.
Hardness tests on materials such as rubber or plastic do not have the same connotation as those performed on metals. The deformation caused by testing such materials may be entirely temporary.
Some hardness tests, especially those intended to provide a measure of wear or abrasion, are performed dynamically with a weight of a certain magnitude dropped from a prescribed height or with a pendulum motion.
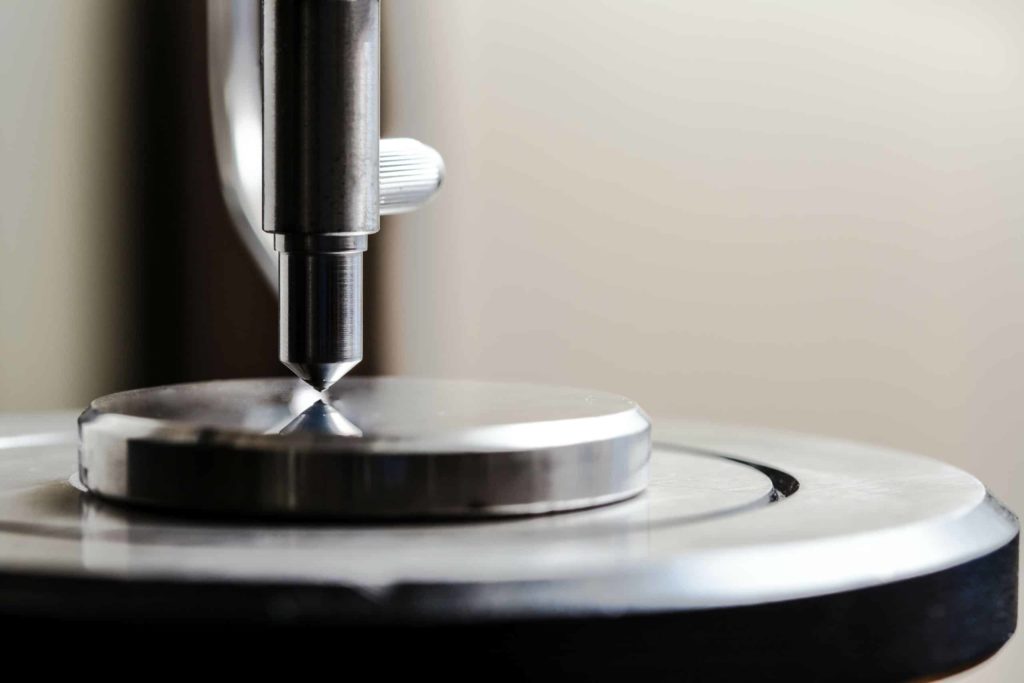
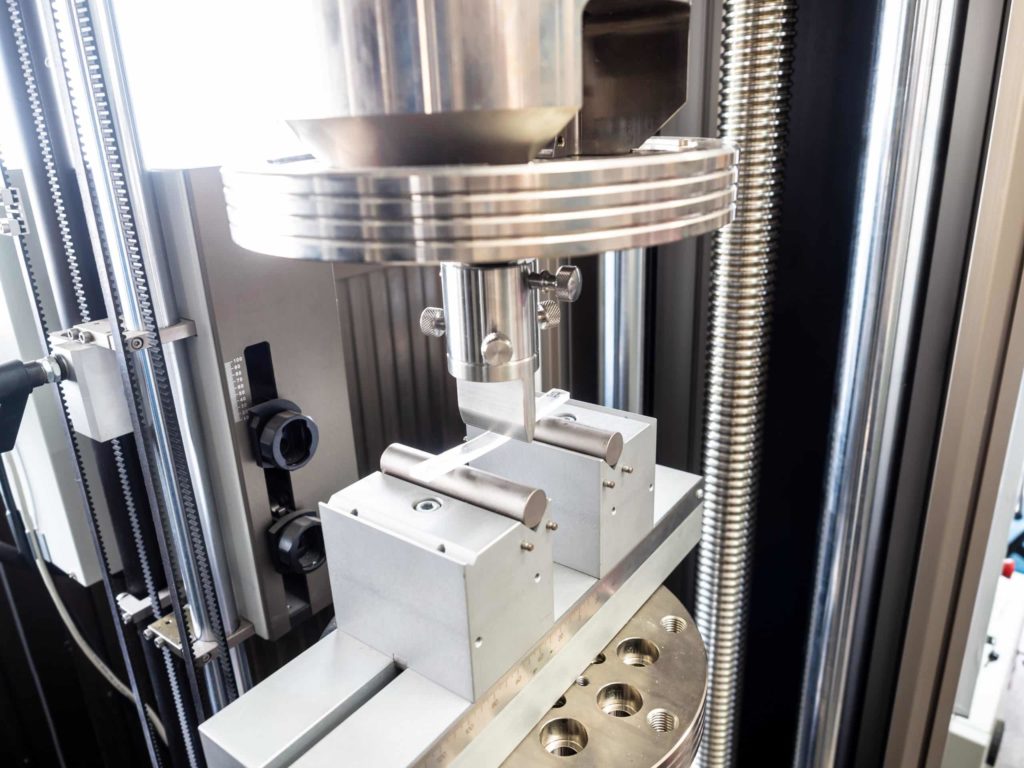
Impact test
Many materials, sensitive to the presence of flaws, cracks and notches, fail suddenly under impact. The most common impact tests (Charpy and Izod) employ a swinging pendulum to strike a notched bar; the heights before and after impact are used to calculate the energy required to fracture the bar and, consequently, the impact strength. Non-metals, such as wood, can be tested as supported beams, similar to the Charpy test.
Some materials vary their impact resistance at different temperatures, becoming very brittle when, for example, they are cold.
Creep test
Creep is the slow change in the dimensions of a material due to prolonged stress; most common metals exhibit creep behavior. In the creep test, loads less than those required to cause instantaneous fracture are applied to the material and the strain is measured over a period of time (creep strain) under a constant load, usually with an extensometer. The time to failure is also measured as a function of stress level; the resulting curve is referred to as stress rupture or creep rupture.
A material that yields continuously under stress and returns to its original shape when the stress is released is said to be viscoelastic; this type of response is measured by the stress-relaxation test. A prescribed displacement or strain is induced in the specimen and the load drop as a function of time is measured.
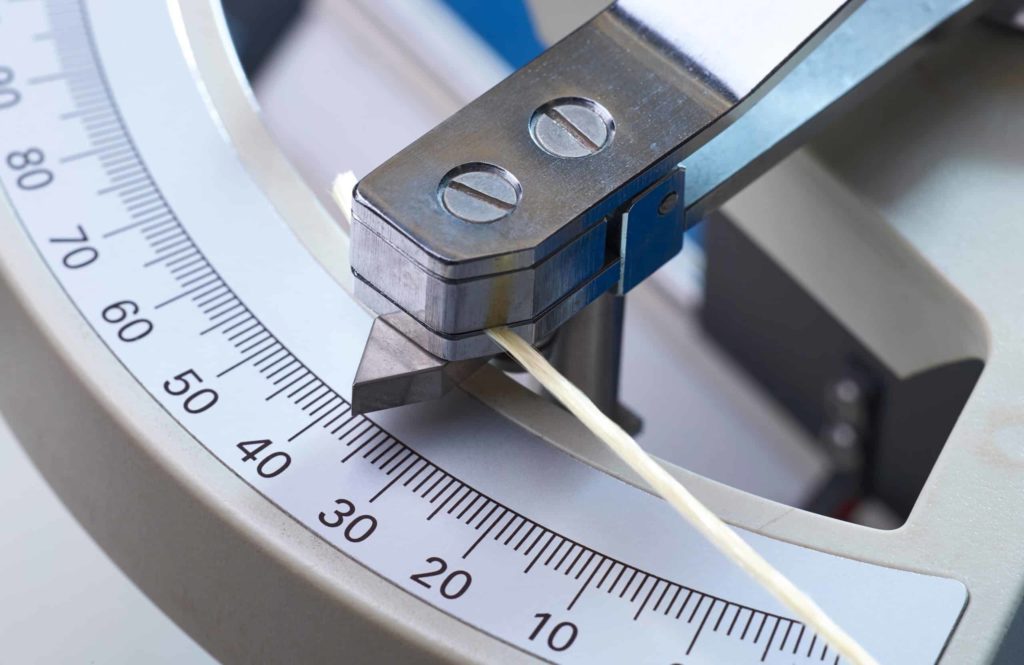
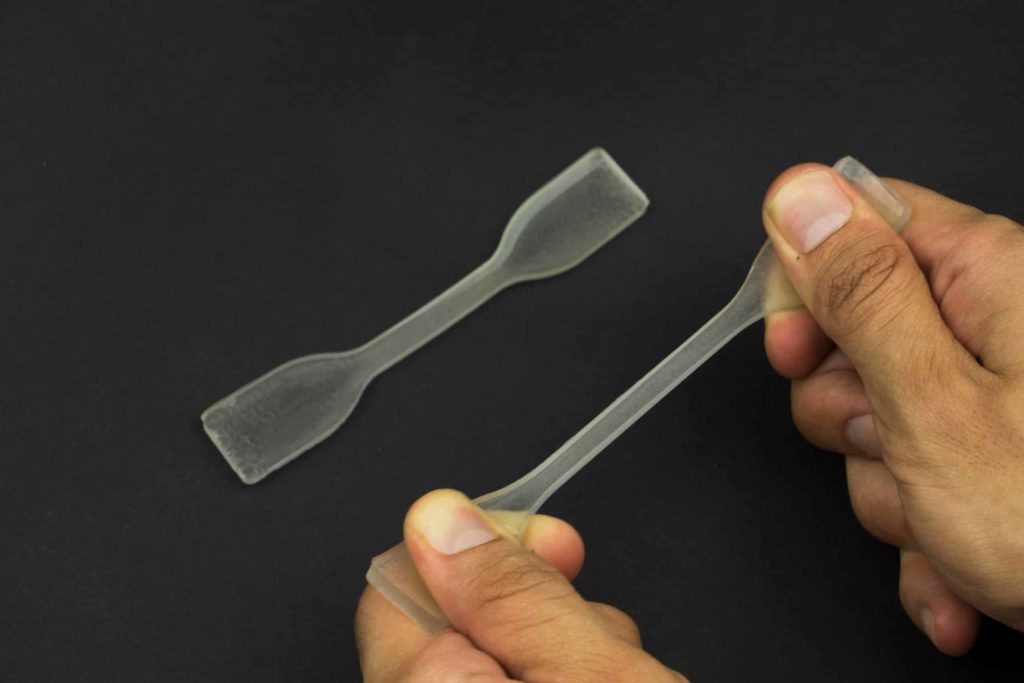
Fatigue tests
Materials that survive a single stress application often fail when subjected to repeated stresses. This phenomenon, known as fatigue, is measured by mechanical tests involving repeated application of different stresses varying in a regular cycle from maximum to minimum value.
The stresses acting on a material in the real world are usually random and non-cyclic in nature. Consequently, several theories of cumulative fatigue damage have been developed that allow researchers to extrapolate from cyclic test data a prediction of material behavior under random stresses. Testing laboratories put this into practice, for example, by performing wear and flaw simulation test on components , which consist of the mechanical application of random fatigue stresses, statistically adjusted to real-life conditions.
Material fatigue involves a number of phenomena, including atomic slip, crack initiation and crack propagation. Therefore, a fatigue test can measure the number of cycles required to initiate a crack, as well as the number of cycles until failure occurs.
In conclusion, we can state that mechanical testing of materials is indispensable in predicting the behavior of materials, preventing failures and providing solutions.
In that sense, Infinitia handles a wide range of testing services, adaptable and tailor-made, to evaluate the mechanical properties of materials. These will be tested, in addition, with first class technological equipment. Contact our experts without obligation to ensure the proper functioning and safety of your materials.
Contact with us
receive a tailored professional response