What was the challenge or problem to solve?
The customer’s high safety concerns at one stage of production led him to contact us for a test to replicate real conditions. The customer had noted a potential hazard and the likelihood of ignition of the system during laser marking in the presence of flammable gases.
As there was no norm or standard to follow, a customised test had to be carried out to simulate real conditions.
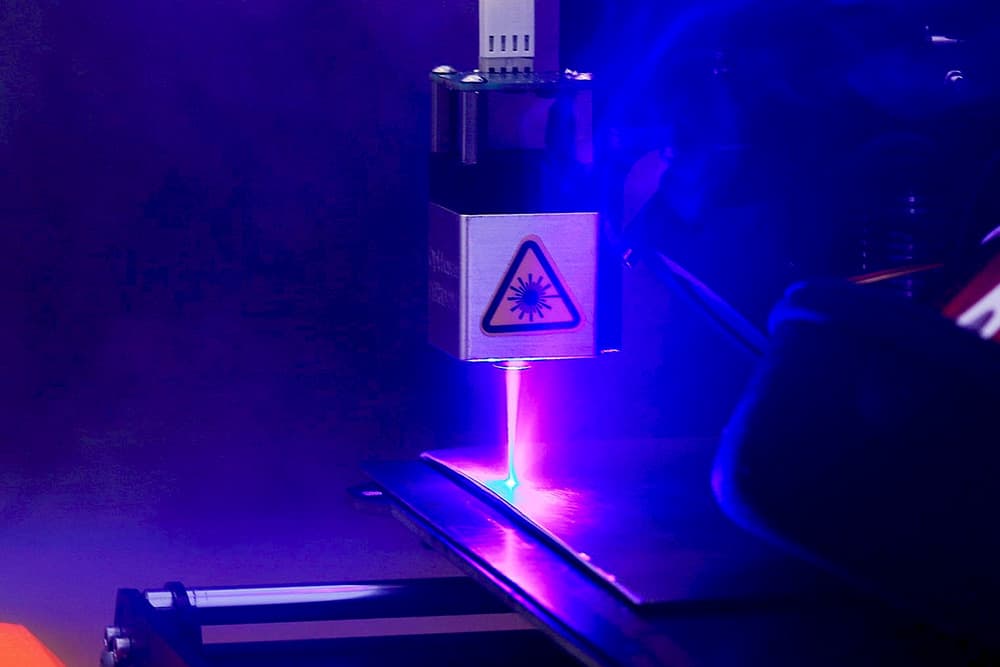
The test was successfully concluded, as the most extreme scenarios that could occur during laser marking were reproduced, providing the customer with valuable information to assess the risk and apply the appropriate measures in production.
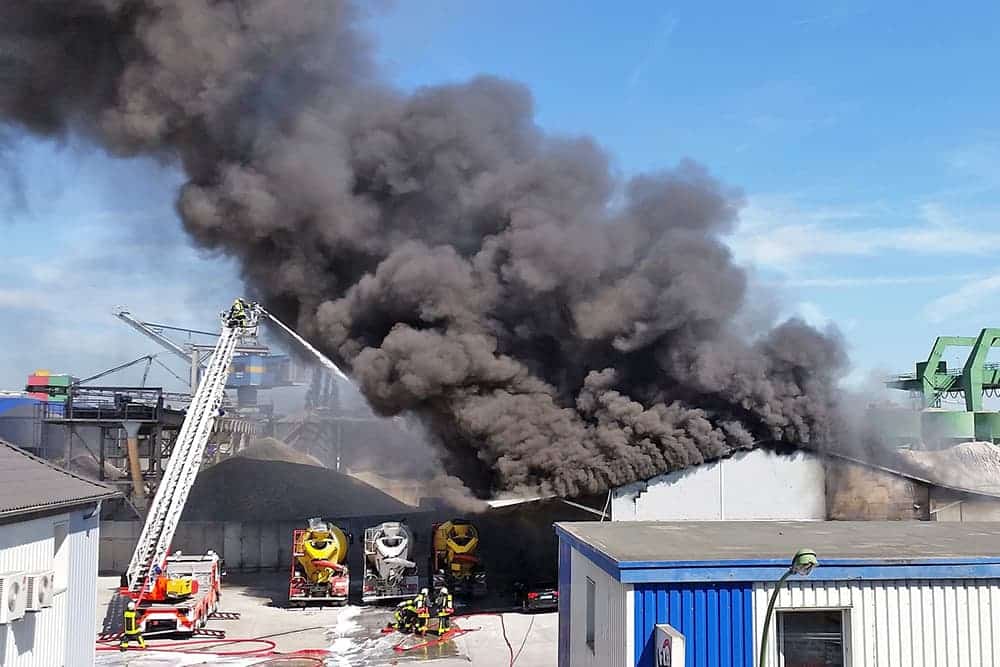
Due to the complexity and high hazard of the study, it was necessary to design, manufacture and assemble a surface with the necessary protective measures and, at the same time, meet the client’s requirements for laser marking the samples. We tackled this phase of the project in detail, checking the correct functioning of the prototype and making the corresponding variations, with the aim of ensuring its functionality and safety.
We then analysed the laser marking according to the customer’s specifications. This allowed us to establish the most suitable parameters for the correct marking of the material.
The next step was to study the process in an atmosphere similar to that proposed by the customer, i.e. in an environment with flammable gases. In order to make an accurate risk assessment, it was necessary to reproduce the most extreme or worst case scenarios.
Based on this information, we evaluated and interpreted the results by rigorously analysing the images taken during the processes. This allowed us to guarantee the reliability of the study and provide the client with a comprehensive assessment report and recommendations to be applied in the factory.