What was the challenge or problem to solve?
As a development for a client, the Product Development team was tasked with the design and manufacturing of an automatic rotating platform for samples, which not only had to stand out aesthetically but also function at a specific speed to optimize the visualization of various samples.
This project had the additional objective of incorporating a structure for a microscope, enhancing the overall aesthetics and providing protection to the equipment. The complexity lay in achieving a constant and adequate rotation of the platform, which had to include several accommodations for the samples while keeping it attached to the microscope structure and concealing the electronics to enhance the visual presentation of the set.
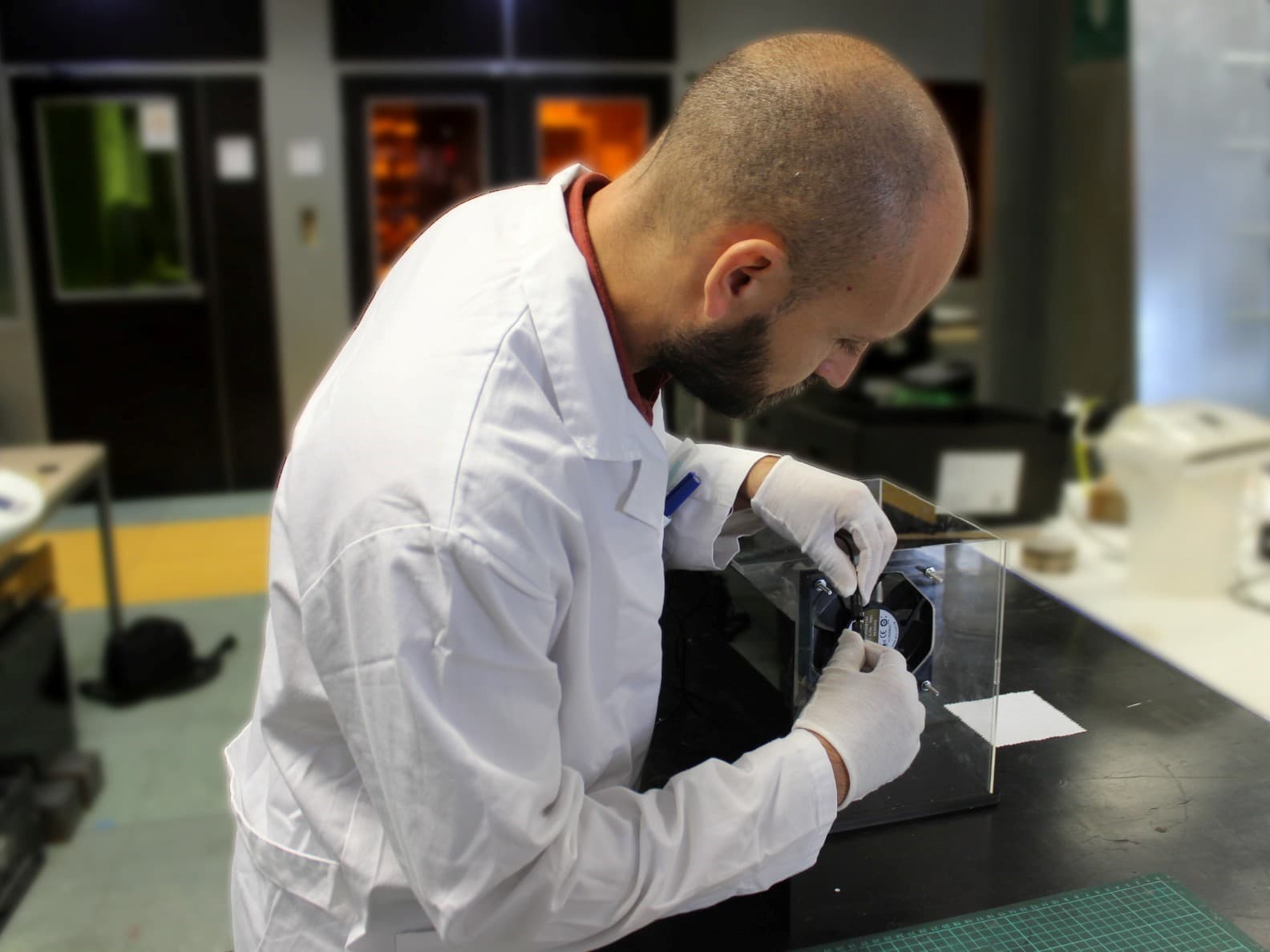
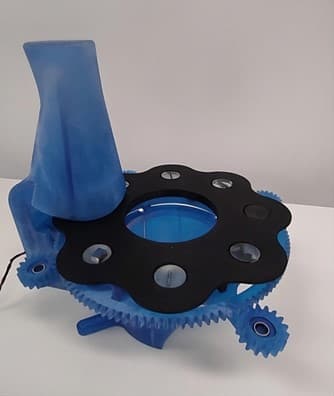
The process began by taking measurements of the samples and the microscope using metrology tools. This initial step was necessary to ensure that the design of the accommodations on the platform and the microscope housing met the necessary specifications for seamless integration.
Subsequently, the 3D design of all components was carried out using professional CAD software to model the rotating platform and the microscope structure. This phase was vital for the visualization and validation of the design, ensuring that all parts fit together harmoniously.
The manufacturing of the prototype through 3D printing was the next step. Using FDM and DLP printers, the various parts of the set were created, allowing the team to physically evaluate the design and make precise adjustments. 3D printing provided the necessary flexibility to experiment with complex geometries and dimensions, speeding up the development process.
The development of the electronics to achieve the desired rotation speed was a key technical challenge. This adjustment was essential to ensure that the platform rotated steadily and at the correct speed, a critical aspect for the functionality and aesthetics of the project.
The project culminated with the assembly of all parts and the validation of their operation. This final step involved the integration of the electronics, the assembly of the platform and the microscope structure, and the verification that the samples fit perfectly into the designed accommodations.
The delivery to the client marked the success of the project, carried out only after verifying the full operation of the system and meeting the technical and aesthetic requirements requested.