What was the challenge or problem to solve?
Topological optimization is a very useful tool to improve the design of metal parts, reduce the weight of components without compromising their mechanical resistance, and even their cost.
This project arose from the need of one of our clients to reduce the total weight of a tool in which a key metal piece is used. This piece was the heaviest element of the assembly and posed a problem for the transport and handling of the tool.
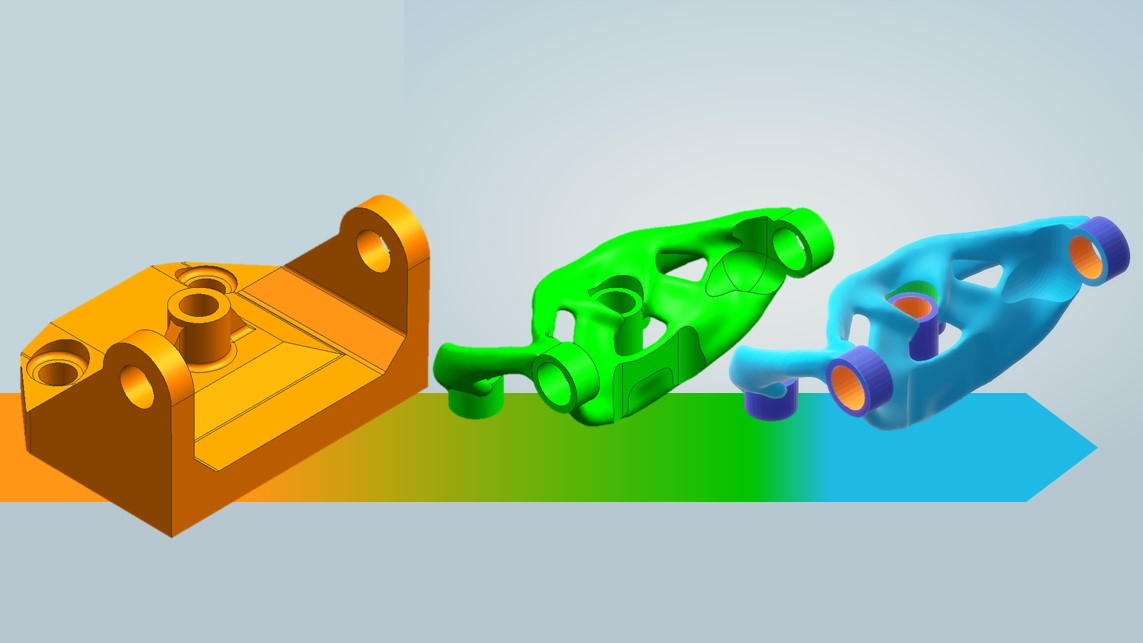
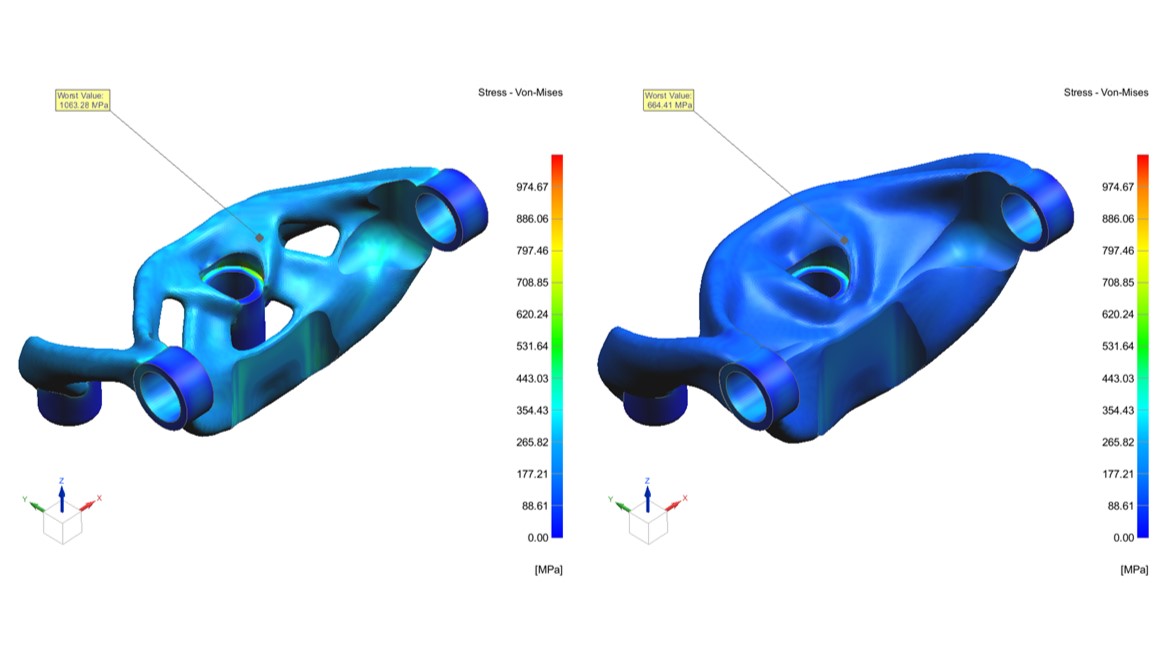
To achieve this goal, our Product Development team began by performing an FEM simulation of the piece to determine its original theoretical functioning. For this, the necessary data such as load weights, relative movements, relative positions, and operation cycles were measured and collected. Then all this information was synthesized and simulated by computer.
This first step was necessary to know the starting point. You cannot improve something of which you do not have enough information.
Next, the model for the topological study was devised, based on the conclusions obtained from the simulation. In addition, different use cases were proposed, and limits on weight and mechanical behaviour were established. Through the topological optimization tool, the maximum design space was created, anchors, available spaces, restrictions, and loads were defined. With the above defined, variables began to be created to feed the tool with enough cases to iterate. To optimize the piece, a starting point had to be created open enough for optimization, but at the same time representative enough of the specific boundary conditions of the piece under study.
Finally, the results obtained after a sufficient number of iterations were compared, and the one that best met all the client’s requirements was selected, which was the one that offered a greater weight reduction while maintaining a mechanical behaviour above the client’s requirements.